Manufacturing the Future
Manufacturing the Future is dedicated to helping manufacturing leaders future-proof their operations. Each episode features interviews with innovative manufacturing executives, subject matter experts, and thought leaders who share actionable insights, tips, and best practices to embrace technology so they can streamline operations, prepare for what lies ahead, and continue to keep the world turning.
Episodes
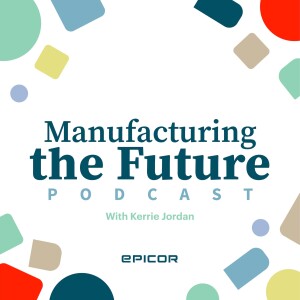
Thursday Jul 03, 2025
Thursday Jul 03, 2025
Meet Zeeshan Zia, CEO & Co-founder of Retrocausal
"If the operator is about to put the tip of the soldering iron at the wrong place, the system offers an alert right there and then, helping them reduce that scrap rate from 30% down to 3%," says Zeeshan Zia, CEO & Co-founder of Retrocausal, describing a process his team helped a medical device manufacturing client improve. His story showcases how enterprise partners want AI that understands human activities, not just fancy interfaces.
Retrocausal tackles the forgotten 80 percent of manufacturing jobs still performed by humans while robotics investments focus on the automated 20 percent. Their AI doesn't replace workers — it catches mistakes like double-torquing bolts while missing others entirely, preventing $1,200 endoscopy cameras from hitting trash bins.
Born from Zeeshan's realization that augmented reality hardware wasn't the bottleneck, Retrocausal decoupled AI capabilities from head-mounted displays. The Seattle company now deploys facial blurring and body pixelation so thoroughly that even strict union environments show the least resistance to their tools compared to other process analytics solutions.
In This Episode
Beyond preventing defects, their platform enables production supervisors to perform industrial engineering tasks through simple video uploads — the AI breaks down processes, generates Excel sheets, and suggests line rebalancing. Zeeshan reflects on how manufacturers have shifted from innovation teams driving AI adoption to plant managers and line leaders becoming true believers, largely thanks to ChatGPT educating the broader public on AI's potential.
Topics
People-centric approach to AI implementation in manufacturing environments that empowers workers rather than replacing them.
Real-world applications of AI copilots including Assembly, Kaizen, and Ergo systems for different manufacturing roles.
Dramatic quality improvements achieved through AI intervention, reducing scrap rates from thirty percent to three percent.
Addressing worker concerns about privacy, standardization, and individual work preferences when implementing AI monitoring systems.
Challenges of implementing AI in high-mix, low-volume job shops versus standardized assembly line operations.
The role of AI in accelerating worker onboarding and enabling career advancement from operator to supervisor roles.
Evolution of manufacturer attitudes toward AI adoption, with investment rates increasing from thirty to forty percent annually.
Importance of choosing holistic AI solutions over point solutions to avoid system fragmentation and integration challenges.
Accessibility features built into AI tools to accommodate workers of different skill levels and physical capabilities.
Impact of reshoring trends and Industry 4.0 on creating new opportunities for AI-enabled manufacturing agility.
Get in touch with Zeeshan Zia:
LinkedIn
Website
Get in touch with your host, Kerrie Jordan:
LinkedIn
Twitter
Download, Listen, and Subscribe
Apple | Spotify | YouTube
Or search “Manufacturing the Future” wherever you listen to podcasts!
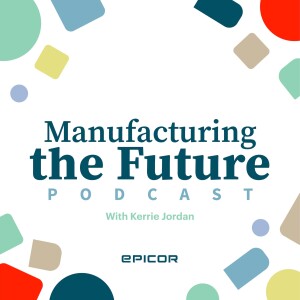
Thursday Jun 26, 2025
Thursday Jun 26, 2025
Meet Alexandre Georgetti, Director of Global i4.0 Automation Strategy at Eaton
"Don't go for a technology just because it's cool. Go for a technology that is going to address a problem," advises Alexandre Georgetti, Director of Global i4.0 Automation Strategy at Eaton, emphasizing the importance of strategic thinking over technological fascination in automation decisions.
Manufacturing organizations worldwide face increasing pressure to automate processes while maintaining workforce engagement and operational efficiency. The challenge lies in identifying which processes to automate first, ensuring successful human-robot collaboration, and implementing technologies that truly solve business problems rather than just adopting the latest innovations.
Eaton, a global power management company operating in more than 175 countries with over 92,000 employees, leads the charge in smart manufacturing adoption. Under Alexandre's leadership, the company's automation strategy spans approximately 200 sites across diverse business units, from electrical components to aerospace systems. This breadth of operations provides unique insights into successful automation implementation across different cultures and manufacturing environments.
In This EpisodeAlexandre shares his expertise on emerging automation technologies, including humanoid robots, collaborative robots with advanced gripping capabilities, and AI-driven learning systems. He emphasizes the importance of maintaining a continuous improvement mindset while implementing automation, and shares practical strategies for ensuring successful human-robot collaboration.
Topics
The evolution of manufacturing automation technologies, including humanoid robots, collaborative robots, and AI-driven learning systems transforming factory operations.
The critical relationship between continuous improvement methodologies and automation implementation for achieving optimal manufacturing outcomes.
Strategies for prioritizing automation projects based on factors including worker safety, value-added activities, and process bottlenecks.
Cultural considerations and regional differences in implementing automation across global manufacturing facilities.
Implementation strategies for autonomous mobile robots in material handling, including considerations for facility-wide compatibility.
The role of data analytics in both planning and optimizing automation initiatives across manufacturing operations.
Balancing automation investments with workforce development to ensure long-term operational success.
Framework development for evaluating and implementing automation technologies across diverse manufacturing environments.
Practical advice for manufacturing leaders beginning or advancing their Industry 4.0 automation journey.
Resources
“Industry 4.0: The factory of the future becomes the factory of today,” from Eaton’s website
Get in touch with Alexandre Georgetti:
LinkedIn
Website
Get in touch with your host, Kerrie Jordan:
LinkedIn
Twitter
Download, Listen, and Subscribe
Apple | Spotify | YouTube
Or search “Manufacturing the Future” wherever you listen to podcasts!
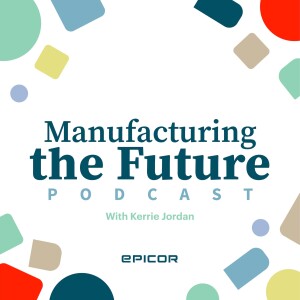
Friday Jun 13, 2025
Friday Jun 13, 2025
Meet Gene Marks, Business Keynote Speaker, Author, Columnist, & Business Owner at The Marks Group
"If you're doing business with China, you've got some serious challenges," warns Gene Marks, Business Keynote Speaker, Author, Columnist, & Business Owner at The Marks Group. As a prolific business columnist for publications like The Guardian and Forbes, and the head of his own company, Gene brings decades of experience helping small and mid-sized businesses navigate economic challenges.
Manufacturing companies today face a perfect storm of challenges: shifting tariff policies creating supply chain uncertainty, rapidly evolving AI technologies demanding implementation strategies, and persistent workforce shortages requiring innovative talent acquisition approaches. Gene addresses all three with practical, tactical advice drawn from his network of successful manufacturing clients across the country.
Gene's journey into business advisory began unexpectedly: he was running his CPA firm when he decided to start writing as a creative outlet. His column for the Philadelphia Business Journal, "The Penny Pincher's Almanac," gained popularity and launched his career as a trusted voice for small and mid-sized businesses. This therapeutic writing practice evolved into a second career spanning prestigious publications and speaking engagements where he shares wisdom gleaned from successful manufacturing companies.
In This Episode
In our wide-ranging conversation, Gene provides immediately actionable strategies for manufacturers dealing with tariffs (like utilizing bonded warehouses to defer costs), a practical three-step approach to prepare for AI implementation (clean your data, engage with vendors, create policies), and unexpected advice on talent acquisition (look for service industry workers with great attitudes who can be trained in technical skills). Gene emphasizes that although technology creates tremendous opportunities, success ultimately depends on having the right people to implement it, making talent acquisition and development perhaps the most critical challenge manufacturers face today.
Topics
Current status of tariffs, particularly the extraordinary 145-185% rates on Chinese goods, and strategies for navigating international trade disruptions.
Strategic use of bonded warehouses and free trade zones to defer tariffs and potentially reduce costs during periods of trade uncertainty.
The reality of AI implementation versus the hype, with practical guidance on current limitations and future potential for manufacturing.
Three essential steps to prepare for AI: cleaning existing data, engaging with software vendors on roadmaps, and developing comprehensive AI policies.
How ERP systems enable data-driven decisions during supply chain disruptions, including selective price increase strategies based on customer profitability.
The critical importance of developing an AI policy governing appropriate usage, permissions, and documentation within manufacturing organizations.
Why small and mid-sized manufacturers must invest in data preparation now to capitalize on AI automation capabilities coming in the next few years.
Innovative approaches to talent acquisition that prioritize attitude, adaptability and customer service skills over technical expertise that can be taught.
Predictions on tariff negotiations and their likely resolution with most countries except China, where manufacturers need long-term alternatives.
The competitive necessity of embracing AI and automation despite employee concerns, with strategies for communicating benefits to the workforce.
Download, Listen, and Subscribe
Apple | Spotify | Google
Get in touch with Gene Marks:
LinkedIn
MediumX
Get in touch with your host, Kerrie Jordan:
LinkedIn
Twitter
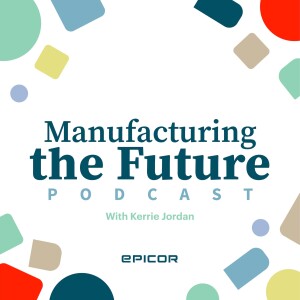
Thursday May 29, 2025
Thursday May 29, 2025
Meet Dan Klepack, Chief Supply Chain Officer at DSG Supply
Drawing from his diverse experience across defense, retail, and industrial distribution, Dan Klepack, Chief Supply Chain Officer at DSG Supply, brings a unique perspective to supply chain modernization. From building fighter jets to leading a supply chain, a process is a process and the disciplines transfer seamlessly. Dan explains, “There's a right way to do it and there's a standard operating procedure that needs to be written to do it.” His journey from manually tracking assembly line performance on paper to leveraging advanced ERP systems demonstrates how technology has fundamentally shifted the focus from data collection to problem-solving.
DSG faces the complex challenge of managing diverse product categories across electrical, plumbing, HVAC, and industrial automation sectors while meeting growing customer expectations for supply chain visibility. Unlike competitors who specialize in single categories, DSG's breadth creates unique operational challenges that require sophisticated technology solutions to balance the competing demands of operations teams seeking repeatability and sales teams needing flexibility.
Founded 125 years ago, DSG operates as an employee-owned company with 62 branches spanning from Montana to Michigan, and leverages Epicor distribution solutions across their business. This employee ownership model creates a distinctive culture where every team member has a financial stake in the company's success, fostering collaborative problem-solving and shared accountability in decision-making processes that impact modernization efforts.
In This Episode
Dan explores how industrial distribution is evolving to meet B2B customers' expectations for the same level of supply chain transparency they experience as consumers. He discusses the industry-wide "Where's My Stuff?" initiative, where competitors collaborate to solve visibility challenges, and shares practical advice on preparing organizations culturally for technology adoption while emphasizing that successful modernization requires understanding your business fundamentals before investing in solutions.
Topics
DSG Supply's employee ownership model and how it influences collaborative decision-making and technology investment strategies across operations.
Evolution of supply chain technology from manual tracking systems to integrated ERP solutions that enable problem-solving focus.
Balancing operational repeatability requirements with sales team flexibility needs through strategic technology implementation and data-driven decision making.
Managing diverse product categories including electrical, plumbing, HVAC, and industrial automation within a single distribution network.
Growing customer expectations for supply chain visibility driven by consumer experience standards applied to B2B relationships.
Industry-wide collaboration through initiatives like "Where's My Stuff?" bringing competitors together to solve shared visibility challenges.
Change management strategies for technology adoption focusing on cultural readiness and team engagement rather than just technical capabilities.
Integration approaches for modern distribution centers emphasizing the importance of understanding business fundamentals before technology investment.
Future trends including artificial intelligence applications across supply chain functions from inventory management to predictive analytics implementation.
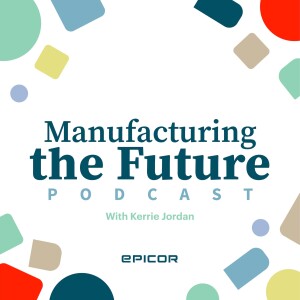
Thursday May 15, 2025
Thursday May 15, 2025
Meet Michael Matisz, Vice President of Supply Chain at Leaf Home
"You have to have a component of quality with all the components of speed," says Michael Matisz, Vice President of Supply Chain at Leaf Home. This philosophy has driven Leaf Home's remarkable transformation from a single-product company to North America's largest home improvement enterprise, serving over 2 million households with solutions from gutter protection to water purification and stair lifts.
The home improvement industry traditionally suffers from lengthy delivery and installation timelines, creating customer frustration and slowing business growth. Michael's team tackled this challenge by developing a revolutionary supply chain model that enables Leaf Home to deliver custom solutions anywhere in the United States within 48 hours, allowing installation within the same business week while competitors might take months to complete similar projects.
Leaf Home's journey began with a simple supply chain for their flagship LeafFilter product, consisting of just 12 SKUs and a few vendors. Michael joined in 2015, and helped establish inventory and supplier management systems that positioned the company for the hypergrowth it would experience during the COVID pandemic. Starting with affordable warehouse and transportation management systems costing just $1,000 annually, the company gradually built more sophisticated operations while maintaining its commitment to rapid customer service.
In This Episode
Michael shares practical wisdom on building resilient supply chains despite economic volatility, treating suppliers as strategic partners rather than just vendors, and balancing inventory positions across a hub-and-spoke distribution network. His engineering background provides a unique perspective on understanding supplier operations, while his retail experience from Joann Stores equipped him to manage exponential SKU growth. He also offers valuable insights on forecasting, sustainability initiatives, and creating supply chains flexible enough to navigate everything from seasonal fluctuations to unexpected tariff changes and interest rate impacts.
Topics
Transforming a simple 12-SKU supply chain into a nationwide network that delivers custom home improvement solutions within 48 hours of order placement.
Building strategic vendor partnerships by "selling" suppliers on your company's growth potential rather than just focusing on procurement negotiations.
Implementing a hub-and-spoke distribution model with six locations across North America to ensure 48-72 hour delivery times nationwide.
Leveraging a manufacturing engineering background to better understand supplier operations and align business needs with manufacturing capabilities.
Balancing inventory positions across multiple distribution centers to optimize speed while managing increased inventory investment costs.
Starting with affordable technology solutions that evolve alongside company growth rather than overinvesting initially.
Navigating volatility in forecasting caused by economic factors like Federal Reserve rate changes impacting customer financing options.
Creating redundancy in the supply chain network to provide flexibility for introducing new product lines and expanding into new geographical markets.
Addressing sustainability initiatives through reverse logistics, lifetime product warranties, and minimizing manufacturing waste in plastic-based products.
Identifying opportunities during supply chain disruptions like tariff changes rather than merely reacting defensively to challenging circumstances.
Meta Description
A conversation with Michael Matisz of Leaf Home about how he built a nationwide supply chain network that delivers custom home improvement solutions within 48 hours, fueling the company's transformation into North America's largest home improvement enterprise.
Get in touch with Michael Matisz:
LinkedIn
Website
Get in touch with your host, Kerrie Jordan:
LinkedIn
Twitter
Listen on WEBSITE
Listen on Apple
Listen on Spotify
Watch on YouTube
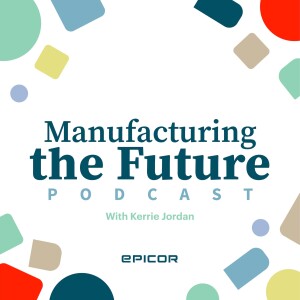
Thursday May 01, 2025
Thursday May 01, 2025
Meet Jeremy Codiroli
"I tell everybody I want to hire on my team that you need to love chaos," says Jeremy Codiroli, VP of Global Supply Chain at AVI-SPL, highlighting his leadership philosophy that has transformed the company's supply chain operations. This embracing of chaos, rather than trying to eliminate it, has become a competitive advantage as his team navigates the complexities of global supply chain management.
AVI-SPL faced significant challenges as a global audio-visual integration company with no dedicated supply chain team. The audio-visual industry traditionally lacked supply chain maturity, with each office handling logistics independently. This fragmented approach created inefficiencies, inconsistencies, and missed opportunities for cost savings and customer satisfaction. Additionally, as the last contractors on job sites, they faced unique scheduling pressures and the risk of technology obsolescence with expensive inventory.
Founded in 1979 and headquartered in Tampa, Florida, AVI-SPL has grown to become the world's largest audio-visual and unified communications integrator, serving 80% of Fortune 100 companies globally. Jeremy joined the company during an acquisition and initially focused on process improvement before recognizing the critical need for dedicated supply chain management. What began as a one-person initiative has rapidly expanded to a global team of over 100 professionals in just 18 months, delivering significant business impact.
In This Episode
In this episode, Jeremy shares how his team is leveraging cutting-edge technologies like AI, including a specialized chatbot for international trade decisions and advanced logistics planning systems. He emphasizes the importance of embracing chaos rather than trying to eliminate it, using data to drive every decision, and maintaining a customer-centric approach that passes cost savings directly to clients. Jeremy also discusses their impressive sustainability initiatives, including a 10% reduction in fleet fuel usage and an innovative "hyper-localized" e-waste program. Throughout the conversation, his passion for creating an "elite supply chain" shines through, demonstrating how supply chain excellence can drive competitive advantage in any industry.
Topics
The importance of embracing chaos in supply chain management rather than trying to eliminate it, creating competitive advantages through adaptability and responsiveness.
How data-driven decision making forms the foundation of all supply chain initiatives, ensuring changes are based on metrics rather than opinions.
The unique challenges of the audio-visual industry, including scheduling pressures as the last contractors on site and the risk of technology obsolescence.
Innovative AI applications including a specialized international trade chatbot trained on company-specific strengths and weaknesses and advanced logistics planning.
The development of a customer-centric supply chain approach that passes cost savings directly to clients and enhances service delivery.
Sustainability initiatives including a 10% reduction in fleet fuel usage and a "hyper-localized" e-waste program that minimizes transportation impact.
Strategies for managing global supply chain complexities across different regions, systems, and capabilities while maintaining consistency.
The importance of upstream data visibility, exemplified by AVI-SPL becoming the first audio-visual integrator to join the Department of Transportation's FLOW program.
Creating a culture of continuous improvement through a no dumb ideas philosophy and the "fail fast, learn fast" approach to innovation.
Meta Description
A conversation with Jeremy Codiroli of AVI-SPL about how he built a data-driven global supply chain organization that embraces chaos, leverages AI innovations, and maintains a customer-centric approach to deliver competitive advantages in the audio-visual integration industry.
Get in touch with Jeremy Codiroli:
LinkedIn
Website
Get in touch with your host, Kerrie Jordan:
LinkedIn
Twitter
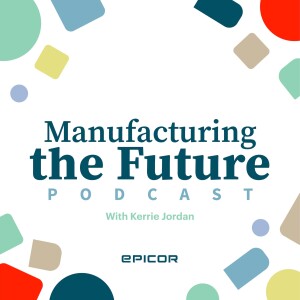
Thursday Apr 17, 2025
Thursday Apr 17, 2025
Meet Mohamed El Shami, CSCO at Garlock Flexibles
"I feel supply chain is like the brain of the operations," Mohamed El Shami, CSCO at Garlock Flexibles. With a background spanning chemical engineering, sales, R&D, and operations, Shami brings a comprehensive perspective to the packaging industry that he describes as "the Switzerland of packaging" — where technical expertise meets operational strategy.
The flexible packaging industry faces significant challenges in balancing sustainability with performance requirements. As consumer demands shift toward more environmentally friendly options, manufacturers must innovate with materials like mono-layers, reduced gauging, and post-consumer-recycled content while ensuring products remain functional. For produce packaging specifically, maintaining freshness for perishable items becomes an additional complexity that impacts every aspect of the supply chain.
Garlock Flexibles has built its reputation over nearly 40 years as a leader in the packaging industry, with a particular strength in the produce market where they supply approximately 60% of salad kits and fresh-cut vegetables in the US. With manufacturing sites in Massachusetts and Nevada, the company has evolved from a family-owned business to their current position under private equity ownership. Their journey reflects the larger transformation of manufacturing in America, balancing domestic production capabilities with global supply chain realities.
In This Episode
In this episode, Shami explores how Garlock navigates post-pandemic supply chain disruptions through diversified supplier relationships, implements sustainability initiatives without compromising product integrity, and prepares for emerging technologies like AI-supported equipment. He emphasizes that successful supply chain management requires understanding the entire product lifecycle, from raw materials to consumer experience, while maintaining profitability for both Garlock and their partners. His insights provide valuable guidance for manufacturing leaders facing similar challenges in an increasingly complex global marketplace.
Topics
The evolution of supply chain management from pre-COVID to post-COVID, shifting from cost efficiency to material availability and supply security considerations.
How the packaging design process balances product protection requirements with sustainability initiatives like mono-material structures and post-consumer recycled content.
The technology behind flexible packaging manufacturing, including the complex printing and laminating processes that create everyday food packaging products.
Strategies for managing inventory and raw materials for produce packaging, where timing is critical due to the short shelf life of the contents.
The importance of building trust and transparency with both domestic and international suppliers while navigating cultural differences and regulatory requirements.
Key metrics for measuring operational excellence, including overall equipment effectiveness, on-time delivery, and maintaining profitability throughout the supply chain.
How the voice of customer feedback directly influences manufacturing processes and supply chain decisions in the packaging industry.
The anticipated impact of AI-supported equipment on manufacturing operations, knowledge preservation, and attracting a new generation of workers.
The balance between just-in-time production and maintaining safety stock inventory in response to global supply chain disruptions.
Approaches to sustainability that include material innovation, structure simplification, and working within existing recycling infrastructure capabilities.
Get in touch with Mohamed El Shami, CSCO at Garlock Flexibles:
LinkedIn
Website
Get in touch with your host, Kerrie Jordan:
LinkedIn
Twitter
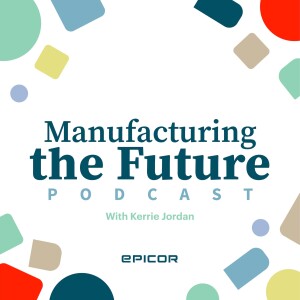
Thursday Apr 03, 2025
Thursday Apr 03, 2025
Meet Michael Krachon, President of Theragenics Interventional
"The manufacturing process itself is challenging because there are really three distinct aspects of it," shares Michael Krachon, President of Theragenics Interventional, in our latest Manufacturing the Future episode. "We have to make the radioisotope itself, then put it into the seeds, and then put the seeds into custom configurations for each patient." This insights-packed conversation reveals the incredible precision required when manufacturing devices smaller than a grain of rice that save lives.
Theragenics tackles a manufacturing challenge like no other: creating medical devices that are tiny, radioactive, and perishable. These brachytherapy seeds, used primarily for cancer treatment, must be manufactured with absolute precision because they'll be implanted directly into patients. The complexity is staggering: managing radiation safety, tracking invisible materials, ensuring perfect quality in something the size of a grain of rice, and dealing with a product that has a limited useful life due to radioactive decay.
Founded over forty years ago, Theragenics has grown into a global manufacturer with one of the country's largest "cyclotron farms" — specialized equipment that creates the radioactive isotopes used in their products. Through multiple acquisitions, including Needle Tech, Galt Medical, and Aerotech, they've diversified their capabilities while maintaining their focus on life-saving medical technology. Over their history, they've manufactured more than 21 million seeds, a massive production volume that, as Michael notes with wonder, "would all fit in almost a cigar box."
In This Episode
In this fascinating conversation, Michael takes listeners behind the scenes of this highly specialized manufacturing operation. From the stringent radiation safety protocols that protect workers to the challenges of supply chain management for components measured in fractions of millimeters, the episode reveals manufacturing excellence at its most precise. Michael also discusses how emerging technologies like AI, targeted robotics, and 3D printing are opening new possibilities for Theragenics while they maintain the extraordinary quality standards necessary when manufacturing devices that patients' lives depend on. It's a rare glimpse into a manufacturing environment where there's no room for error — because getting it right means saving lives.
Topics
The unique challenges of manufacturing radioisotope-based medical devices that are simultaneously tiny, radioactive, and perishable with strict time constraints.
How Theragenics operates one of the country's largest "cyclotron farms" to create radioisotopes that become components in life-saving cancer treatment devices.
The extensive radiation safety protocols and monitoring technologies implemented to protect employees working with radioactive materials.
Managing precise manufacturing processes for implantable medical devices the size of a grain of rice that must be perfectly made every time.
Balancing innovation with strict regulatory requirements in a field where product quality directly impacts patient outcomes and safety.
Supply chain and inventory management strategies for components measured in fractions of millimeters that cannot use traditional tracking technologies.
The impact of COVID-19 on workforce management and the challenges of rebuilding institutional knowledge after experienced staff turnover.
Future technology applications including AI for production planning, targeted robotics for employee safety, and 3D printing for specialized components.
The critical importance of customization in medical device manufacturing, with each cancer patient receiving a uniquely configured product.
Advice for manufacturing leaders about cross-industry learning, relationship building, and engaging directly with technicians to solve manufacturing challenges.
Get in touch with Michael Krachon:
LinkedIn
Website
Get in touch with your host, Kerrie Jordan:
LinkedIn
Twitter
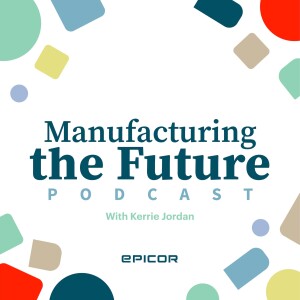
Thursday Mar 20, 2025
Thursday Mar 20, 2025
Meet Lisa Pope, recently retired President and Chief Revenue Officer at Epicor
"I think honestly the number one thing is to be client centric at all costs," says Lisa Pope, recently retired President and Chief Revenue Officer at Epicor, encapsulating the mentorship philosophy that has defined her remarkable 40-year career in software technology. Throughout leadership roles at industry giants including NCR, Oracle, QAD, Infor, and ultimately Epicor, Lisa has cultivated a leadership approach centered on empowering teams and maintaining unwavering customer focus.
Today's technology leaders face unprecedented challenges in navigating digital transformation, particularly as artificial intelligence emerges as what Lisa calls the third wave of ERP evolution. After the Y2K and cloud computing revolutions, AI represents a critical inflection point where software providers must seamlessly integrate this technology into their core systems rather than treating it as an add-on. Companies failing to embrace this change risk falling behind competitors who leverage AI to enhance decision-making and operational efficiency.
Lisa's career journey began unexpectedly when Triad Systems (later acquired by Epicor) recruited her after college, initially placing her in customer-facing roles that instilled a deep appreciation for client perspectives. This foundation guided her through multiple leadership positions across the industry, eventually bringing her full circle to Epicor where she helped drive the company's transformation into a billion-dollar cloud technology leader. Under her leadership, Epicor evolved from reactive customer relationships to deep collaborative partnerships, while simultaneously achieving double-digit revenue growth.
In This Episode
Lisa shares invaluable insights on strategic career planning, including the importance of thoughtful job transitions, the value of lateral moves for gaining broader experience, and practical advice for retirement planning. She discusses how mentorship and building diverse professional networks can accelerate career development, while emphasizing that the most sustainable path to organizational success lies in unwavering customer-centricity. For technology leaders navigating today's rapidly evolving landscape, Lisa's experience offers both practical guidance and inspirational perspectives on creating meaningful impact.
Topics
The evolution of Lisa's 40-year career in software technology, from unexpected beginnings to leading a billion-dollar global enterprise at Epicor.
Strategic approaches to career advancement, including the value of lateral moves to gain broader experience rather than always climbing upward.
The importance of mentorship and building diverse professional networks beyond immediate colleagues to create career opportunities and support.
How artificial intelligence represents the third wave of ERP transformation, following Y2K and cloud computing revolutions in enterprise software.
Practical guidance for retirement planning, including developing a structured approach rather than focusing solely on age or financial milestones.
The transformation of Epicor over eight years from siloed products to integrated solutions, with significant improvements in customer-centricity and financial performance.
Evolution of customer relationships from reactive support to collaborative partnerships, with deeper engagement and value-focused interactions.
Industry consolidation trends and cross-pollination between manufacturing, distribution, and retail sectors creating new competitive challenges.
Work-life balance strategies that incorporate travel and personal interests throughout career development rather than deferring until retirement.
Why unwavering customer centricity at all levels — from frontline staff through executive leadership to the board — remains the cornerstone of sustainable business success.
For more discussion about the future of AI in ERP, check out Arturo Buzzalino, Epicor Chief Innovation Officer, on the SourceForge podcast.
Get in touch with Lisa Pope:
LinkedIn
Get in touch with your host, Kerrie Jordan:
LinkedIn
Twitter
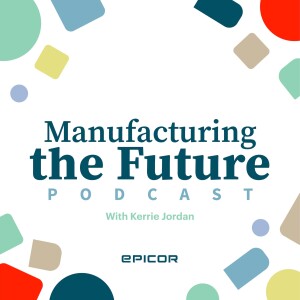
Wednesday Mar 05, 2025
Wednesday Mar 05, 2025
Meet Alexej Kinderknecht, President & Technical Director of MRU Instruments
"Support is what we learned over the last couple of years," reflects Alexej Kinderknecht, President & Technical Director of MRU Instruments, emphasizing how technical innovation must be matched with exceptional customer service to truly transform manufacturing efficiency.
In today's manufacturing landscape, companies face the dual challenge of optimizing their operations while meeting increasingly stringent environmental requirements. This intersection of efficiency and environmental responsibility demands precise, reliable emissions monitoring solutions that can deliver accurate data while being robust enough to handle the harsh conditions of industrial environments.
Alex's journey with MRU Instruments spans over 16 years, starting as an intern in manufacturing before moving through R&D and service roles. His path to leadership was driven by a passion for efficiency and continuous improvement, eventually leading him to oversee US operations where he combines technical expertise with a deep understanding of customer needs.
In This Episode
The episode explores how precision-engineered analyzers are revolutionizing everything from home heating efficiency to industrial-scale emissions monitoring. Alex shares insights on balancing innovation with practical implementation, the critical importance of customer support in technical solutions, and why accuracy in emissions monitoring directly impacts both environmental compliance and operational costs. His perspective highlights how the right combination of technical excellence and customer support can transform environmental requirements from mere compliance issues into opportunities for significant cost savings and operational improvements.
Topics
The evolution of emissions monitoring technology from basic analysis to precision-engineered solutions that help optimize operational efficiency and reduce costs.
The critical role of customer support and practical implementation in ensuring the successful adoption of new monitoring technologies.
How accurate emissions monitoring can lead to significant cost savings by optimizing combustion processes and reducing unnecessary fuel consumption.
The importance of balancing rapid response to urgent customer needs with long-term technology development and innovation.
Strategies for implementing new monitoring technologies while ensuring both regulatory compliance and practical usability for customers.
The impact of EPA regulations and environmental requirements on the development of new monitoring solutions and customer support needs.
How starting as an intern and working through various roles provides valuable perspective for leading technical innovation and customer support.
The relationship between accurate emissions monitoring, cost savings, and environmental compliance in modern manufacturing operations.
The future of emissions monitoring technology and the increasing importance of support services in technical solution implementation.
Building customer trust through reliable products and responsive support services in the specialized field of emissions monitoring.
Get in touch with Alex Kinderknecht:
LinkedIn
Website
Get in touch with your host, Kerrie Jordan:
LinkedIn
Twitter
Download, Listen, and Subscribe
Apple | Spotify | Google
Or search “Manufacturing the Future” wherever you listen to podcasts!